University of Pennsylvania
UPenn Upgraded Lab Exhaust Saves Almost $2M in Yearly Operating Cost
Background:
The University of Pennsylvania is a leading center for molecular research, with a broad array of buildings to facilitate experimentation and inquiry. To maintain optimal research capacity as well as reduce on-campus energy use, the school administration renovated the 1973 Wing (Chem 73) of the university’s largest laboratory complex.
The building’s 65 chemistry labs were a true energy burden due to their constant-volume exhaust operation. More than 104 belt-driven exhaust fans ran non-stop, 365 days a year. Chem 73 was conditioning and exhausting more than 280,000 CFM* at all times.
Over the years, there had been a few Band-Aid projects in an attempt to curb the energy use, but none made a noticeable difference. “If you consider that it costs us roughly $10 per CFM per year, ventilation at Chem 73 had an annual expense of nearly $3 million,” said Dan Burke, Sr. building administrator. “That doesn’t include maintenance of the system, either.”
Furthermore, offices and labs were uncomfortable, and in some rooms, exhaust noise was so loud that speaking at normal volumes wasn’t possible. Faculty also wanted less temperature fluctuation within the laboratories; an advantage during many processes. The university needed a retrofit to change the exhaust system from CAV (constant air volume) to VAV (variable air volume); nothing less would yield acceptable results.
The Situation
In the Fall of 2011, a feasibility study began with consulting engineers to help identify how to retrofit Chem 73’s systems to save energy. Roger Fournier, project manager for AHA, and Milt Kirkman, president of The Kirkman Oliver Company, a manufacturer’s representative firm based in Newtown Square, PA were part of the team that recommended not only converting from constant to variable air volume, but also complete infrastructure upgrades.
“It was obvious that a VAV approach was needed,” said Fournier. “What wasn’t immediately apparent was how best to update or replace fume hoods across seven different floors, remove and replace the old exhaust fans and replace the air handling units, all while the building was occupied and research continued safely.”
Of the 137 fume hoods, 82 are original from 1973. Other hoods were added over the decades since, with varying ages and a variety of control systems. Kirkman suggested retrofitting all the hoods for VAV operation instead of replacing them entirely. This would save the university about $20,000 per hood, but required a little extra effort.
While the oldest hoods could be easily retrofitted with Phoenix Controls monitoring equipment designed specifically for the application, the hoods would need to pass ASHRAE 110 testing. A Beta Test was proposed and a single hood outfitted with new controls. When tested by an independent third party, it passed with flying colors. This was the final green light for renovations at Chem 73.
The Solution
All 137 fume hoods in the building would be retrofitted to accommodate fluctuating exhaust levels, and to turn back automatically if the work space is unoccupied. This includes installation of Phoenix Controls Zone Presence Sensors® (also known as ZPS® sensor), Phoenix Controls fume hood monitors (FHMs), and Phoenix Controls venturi valves.
Before any fume hoods were decommissioned, six new high-plume exhaust fans were mounted on the roof and connected to a plenum that spanned both existing fan towers. Under normal operating conditions, the new system will eliminate 182,000 CFM of unnecessary airflow while maintaining peak airflow capability in the event of an emergency. The result is an energy savings of roughly $1.8 million in an average year.
The retrofit began in September of 2013. While the work was broken into phases in order to maintain occupancy for the duration, work never ceased between phases. At most, four labs were closed at a time, and never for longer than a week.
“We used 521 Phoenix Controls venturi valves throughout the building,” said Fournier. “The flow rates may have required only 8”, 10” or 12-inch valves, but we selected 14-inch valves for their available turndown rate; from 2,500 to 200 CFM. Also, going with 14s gives the university some flexibility to expand the labs in the future; a big advantage for the marginal cost increase between the sizes.”
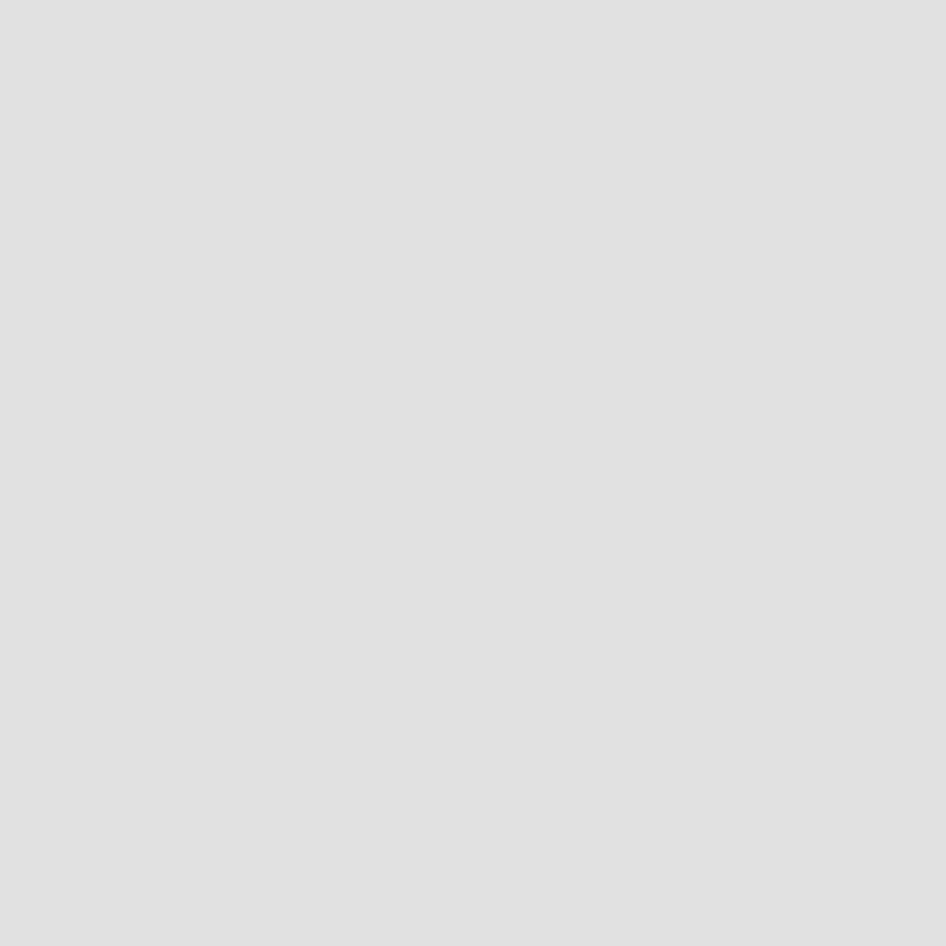
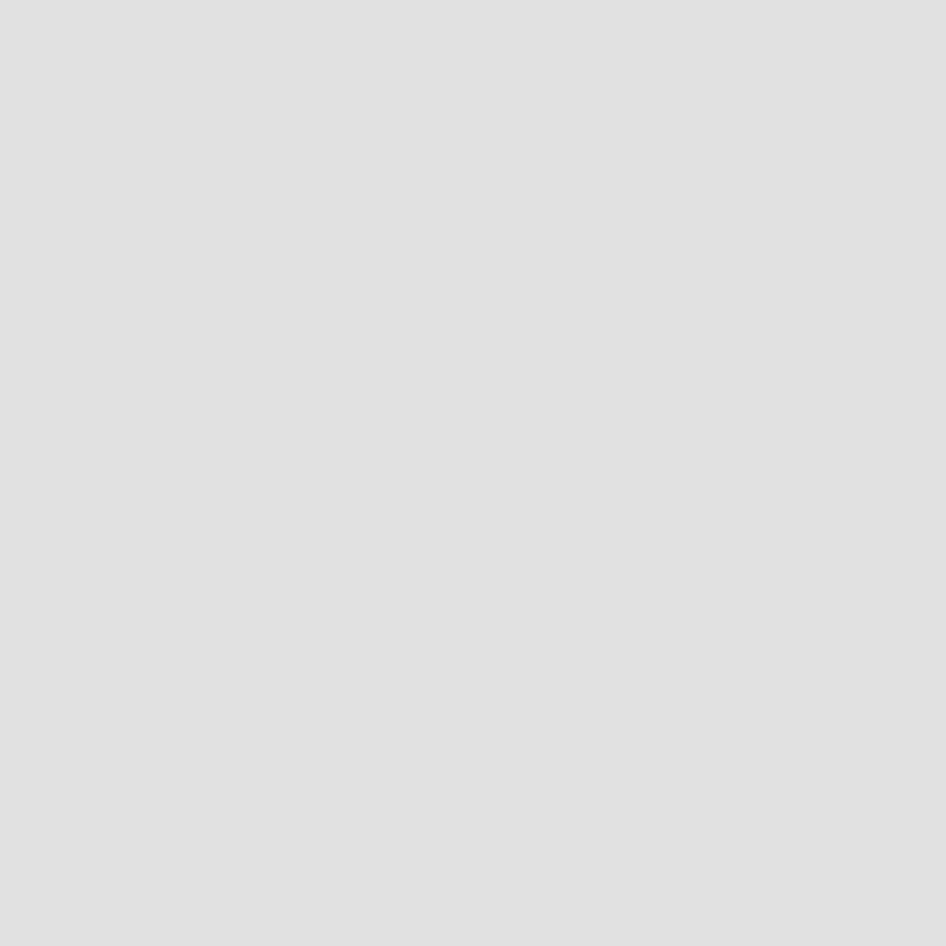
The Result
By simply changing the way that air is moved through Chem 73, the university expects to shrink energy expenses by nearly $2 million annually. But everyone involved wanted more accurately quantify the energy reductions.
The building’s August power consumption fell from 735,000 kWh in 2013 to 447,000 kWh after the retrofit in 2014, a reduction of almost 40 percent**.
“I used to deal with a dozen fume hood failures each week,” said Burke, who was an HVAC technician before taking a job at the university. “I’ve not had a single complaint or problem since the new Phoenix Controls were installed.”
When finished in August of 2014, the retrofit came in five percent under budget and one month ahead of schedule.
Building occupants share a similar sentiment. Regardless of outdoor conditions, the temperature in the labs holds within ¼ of a degree of setpoint, and outstanding feat for a 40-year old building. And the fume hoods are safer and more user friendly than ever. Noise in the labs was reduced so drastically that several researchers were concerned that the hoods weren’t even operating.
*The CFM value is taken from building management tracking.
**Electrical savings is a total value that includes fans and chilled water electrical use, also factoring in heat recovery and use unaffected by this project - such as process load.
The ZPS sensor - Identifies occupancy in front of the fume hood. When the fume hood is unoccupied the face velocity and airflow is turned down and reduced by 40%. When the fume hood becomes occupied, the face velocity is increased to its specified level; creating a safe environment for the researcher and a significant opportunity to save energy.
The FHM - Supports additional energy saving benefits at the fume hood; providing visual and audible indications of face velocity and fume hood status. Especially for energy savings, the FHM provides an indication of energy waste based on sash position or if the sash has been left open. It can also put an unused fume hood into hibernation mode, if no chemicals are being stored in the hood cabinet or in the hood itself.